این مقاله یک راهنمای فنی جامع با هدف ارائه تحلیلی دقیق از مشخصات، مزایا، محدودیتها و ملاحظات طراحی و اجرایی مرتبط با لوله پلی اتیلن فشار قوی نفت (گرید PE100) است. دامنه این راهنما، کاربرد های مختلف این محصول در بخش های بالا دستی، میان دستی و پایین دستی صنعت نفت و گاز را پوشش میدهد. هدف اصلی، فراهم آوردن یک منبع اطلاعاتی قابل اتکا برای مهندسان طراح، مدیران پروژه، متخصصان تدارکات و کارشناسان بهره برداری به منظور اتخاذ تصمیمات آگاهانه در زمینه انتخاب و خرید لوله فشار قوی خطوط لوله کشی است.
چالش های تاریخی خطوط لوله فلزی در صنعت نفت و گاز
خطوط لوله فولادی برای سالهای متمادی به عنوان استاندارد اصلی در این صنعت مورد استفاده قرار گرفتهاند. با این حال، استفاده از آنها همواره با چالشهای مهندسی قابل توجهی همراه بوده است که بر هزینه کل مالکیت (TCO) و ریسکهای عملیاتی تاثیر مستقیم دارد. این چالشها عبارتند از:
خوردگی:
خوردگی داخلی ناشی از سیالات فرآیندی (نفت، گاز، آب شور، H2S, CO2) و خوردگی خارجی ناشی از عوامل محیطی، بزرگترین عامل کاهش عمر مفید و شکست خطوط لوله فولادی است.
هزینههای نگهداری بالا:
نیاز مستمر به بازرسی، تعمیر و نگهداری سیستم های حفاظت از خوردگی (پوششها و حفاظت کاتدی) بخش قابل توجهی از هزینه های عملیاتی را به خود اختصاص میدهد.
وزن بالا و لجستیک پیچیده:
حمل و نقل و نصب لولههای فولادی نیازمند تجهیزات سنگین و هزینه های لجستیکی بالاست که به افزایش هزینه هیا سرمایهای اولیه (CAPEX) منجر میشود.
عدم انعطاف پذیری:
سختی و عدم انعطاف پذیری فولاد، آن را در برابر تنش های ناشی از جابجایی خاک و بارهای لرزهای آسیب پذیر میکند.
معرفی پلی اتیلن گرید PE100 به عنوان یک ماده مهندسی پیشرفته
در پاسخ به این چالشها، علم مواد، پلیمرهای مهندسی پیشرفتهای را معرفی کرده است. پلی اتیلن با چگالی بالا (HDPE) گرید PE100، یک ترموپلاستیک مهندسی شده است که به طور خاص برای کاربردهای تحت فشار بالا و شرایط سخت محیطی طراحی شده است. این ماده به دلیل ترکیب منحصر به فردی از خواص فیزیکی، مکانیکی و شیمیایی، به عنوان یک راهکار کارآمد برای غلبه بر بسیاری از محدودیتهای مواد فلزی سنتی مطرح شده است.
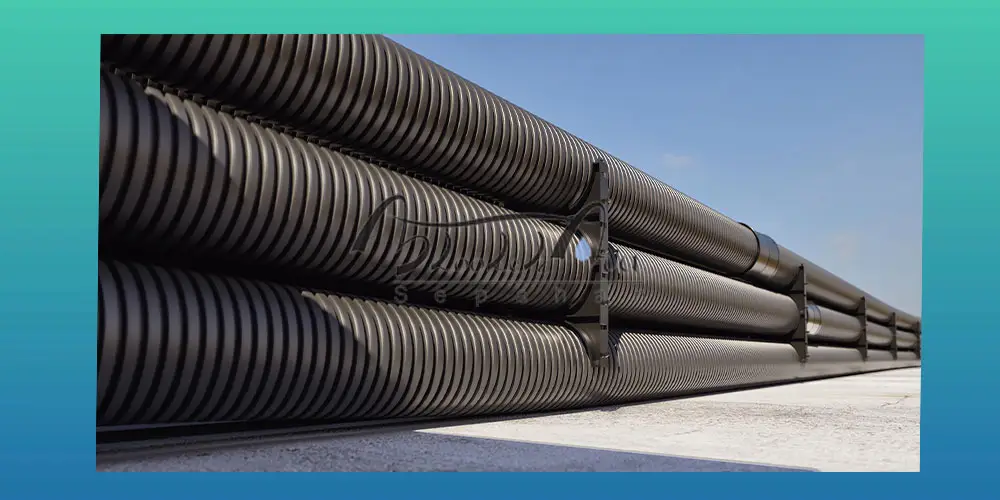
مشخصات فنی و علم مواد
ساختار شیمیایی و ساختار مولکولی لوله های نفت و گاز
پلیاتیلن (PE) از پلیمریزاسیون مونومر اتیلن (C₂H₄) حاصل میشود و ساختار آن متشکل از زنجیره های طولانی هیدروکربنی است. در نوع HDPE، این زنجیره ها عمدتاً خطی بوده و بلورینگی و چگالی بالایی ایجاد میکنند که به بهبود خواص مکانیکی مانند استحکام کششی و سختی منجر میشود.
دستهبندی گریدها: PE80، PE100 و PE100‑RC
لوله های پلیاتیلن بر اساس «مقدار مقاومت اسمی» (MRS) طبقه بندی میشوند:
PE80: MRS برابر با ۸٫۰ مگاپاسکال؛ مناسب سیستم هایی با فشار کاری متوسط.
PE100: MRS برابر با ۱۰٫۰ مگاپاسکال؛ با استحکام بالاتر امکان استفاده از دیواره های نازک تر را فراهم میکند و به صرفه تر است، به ویژه در شبکه های نفت و گاز پرفشار.
PE100‑RC (Resistant to Crack): نسل پیشرفته ای از PE100 با مقاومت بسیار بالا در برابر گسترش ترک های ریز (SCG)، ایده آل برای شرایط نصب بدون حفاری یا بستر نامناسب که تمرکز تنش و ساییدگی رخ می دهد.
خواص فیزیکی و مکانیکی کلیدی لوله های فشار قوی نفت و گاز
در جدول زیر مهمترین مشخصات گرید PE100 آورده شده است:
خاصیت | مقدار نمونه | توضیحات |
---|---|---|
چگالی (Density) | ۰٫۹۵ – ۰٫۹۶ g/cm³ | چگالی بالا بهمعنای استحکام و سختی بیشتر است. |
شاخص جریان مذاب (MFI) | ۰٫۲ – ۱٫۴ g/۱۰min | نشاندهنده ویسکوزیته مذاب و قابلیت فرآیندپذیری. |
مدول الاستیسیته (Modulus) | ۸۰۰ – ۱۲۰۰ MPa | بیانگر سختی ماده؛ مدول پایینتر، انعطاف پذیری بیشتر. |
استحکام کششی در تسلیم (Yield) | ≥ ۲۰ MPa | بیشینه تنش قبل از تغییر شکل پلاستیک. |
ازدیاد طول در پارگی (Elongation) | > ۶۰۰٪ | دلالت بر چقرمگی و انعطاف پذیری فوقالعاده. |
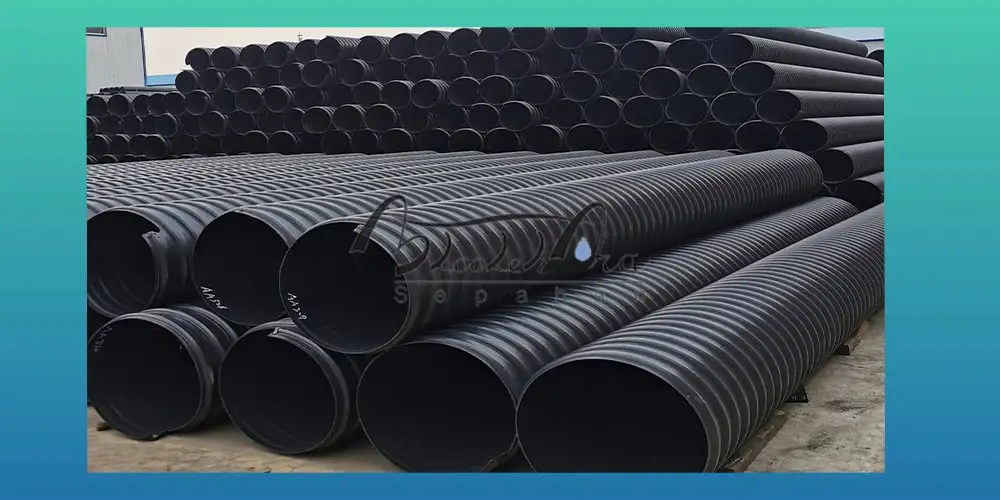
رفتار حرارتی صنعت نفت و گاز
دامنه دمای کاری: معمولاً از –۲۰ تا +۶۰ درجه سانتیگراد. در دماهای بالاتر باید با در نظر گرفتن ضریب کاهش (Derating Factor) فشار کاری را تصحیح کرد.
ضریب انبساط حرارتی: تقریباً ۱٫۴×۱۰⁻⁴ m/m/°C که بسیار بیشتر از فلزات است و در خطوط بالای زمین نیازمند ملاحظات طراحی برای کنترل انبساط و انقباض است.
نقش افزودنی ها
برای پایداری در مقابل اشعه ماوراء بنفش و افزایش ماندگاری، معمولاً ۲–۲٫۵٪ وزنی کربن بلک (Carbon Black) به پلیاتیلن افزوده میشود. این افزودنی ضمن محافظت در برابر تخریب ناشی از UV، خواص مکانیکی را نیز حفظ میکند و از آسیب سطحی جلوگیری مینماید.
تحلیل همه جانبه مزایای عملکردی و اقتصادی
تاب آوری در برابر خوردگی لوله های نفت و گاز
مصونیت الکتروشیمیایی
پلیاتیلن مانند سپری نامرئی بر فلزات عمل میکند؛ دیالکتریک بودن آن هرگونه واکنش گالوانیک یا الکترولیتی را خنثی میکند و خورندگی را از ریشه بخشکاند.
مقاومت شیمیایی بی همتا
HDPE با مهربانی یک نگهبان، در برابر سیل بیرحم اسیدها، بازها، نمکها و عوامل خورندهی نفت و گاز (H₂S، CO₂، آب شور و…) بی تزلزل ایستادگی میکند.
ثمرات اقتصادی
این پایداری ذاتی، انبان هزینههای گزاف CAPEX و OPEX مربوط به پوشش های محافظتی، حفاظت کاتدی، تزریق بازدارنده ها و بازررسی های مکرر را برچیده و سرمایه شما را در مسیر سازندگی هدایت می کند.
یکپارچگی بی بدیل و آب بندی مطلق
جوش بات فیوژن
دو لبهی لوله، در آغوش صفحهای داغ ذوب میشوند و با فشار یکپارچهای به هم میپیوندند؛ پیوندی همسان و حتی قوی تر از خود لوله.
جوش الکتروفیوژن
در این رقص تکنولوژیک، سیم پیچ های حرارتی داخل اتصالات با جادوی برق ذوب را رقم میزنند و دست به پیوندی زوال ناپذیر میزنند، ایدهآل برای فضاهای تنگ و پرچالش.
نتیجهی نهایی
سیستمی کاملاً مونولیتیک، بدون کوچک ترین نشتی که تکیه گاهی استوار برای ایمنی و پاکی محیط زیست فراهم میآورد.
رفتار دینامیک و قدرت مکانیکی
انعطاف به وسعت خلاقیت
مدول الاستیسیتهی پایین HDPE، به لولهی فشارقوی اجازه میدهد بنایش را تا ۲۰–۲۵ برابر قطر خود خم کند،بی نیاز از هرگونه زانو و اتصالات اضافی.
استقامت در برابر خستگی
وقتی فشار متغیر بارها بر جسم لوله میتازد، این ماده با خونسردی از عمری طولانی در برابر چرخه های پرفشار حفاظت میکند.
فرمانبرداری لرزهای
در زلزلههای بی رحم، HDPE همچون سپر انعطاف پذیر انرژی امواج را می بلعد و از خود و بستگانش، شبکهی لولهکشی را حفظ میکند.
سایش ناپذیری لوله های پلی اتیلن نفت و گاز
در نبرد جریان های دوغاب و ذرات ساینده، HDPE بر فولاد کربنی چیره میآید و دیواره ها را در برابر خوردگی مکانیکی بیمه میکند، مناسب انتقال نفت خام ماسهآلود، پساب حفاری و آب های تولیدی.
بهینگی هیدرولیکی
دیوار داخلی صیقلی HDPE با ضریب زبری حدود ۱۵۰ و تقریباً ۰٫۰۰۹، تا پایان عمر سرویس ثابت میماند. نتیجه؟ افت فشار اندک و قبض انرژی پمپ تان که هیچگاه سربهفلک نمینشیند.
سادگی لجستیک و نصب
سبکی لوله های فشار قوی حدود یکهشتم وزن فولاد، در واقع یورش هزینه های حملونقل را خنثی میکند، همچنین نیاز به ماشینآلات سنگین را بهکلی از میان برمیدارد و سرعت عملیات نصب را به اوج میرساند. این همه یعنی کاهش محسوس CAPEX و آغاز پروژهای پرشتاب است.
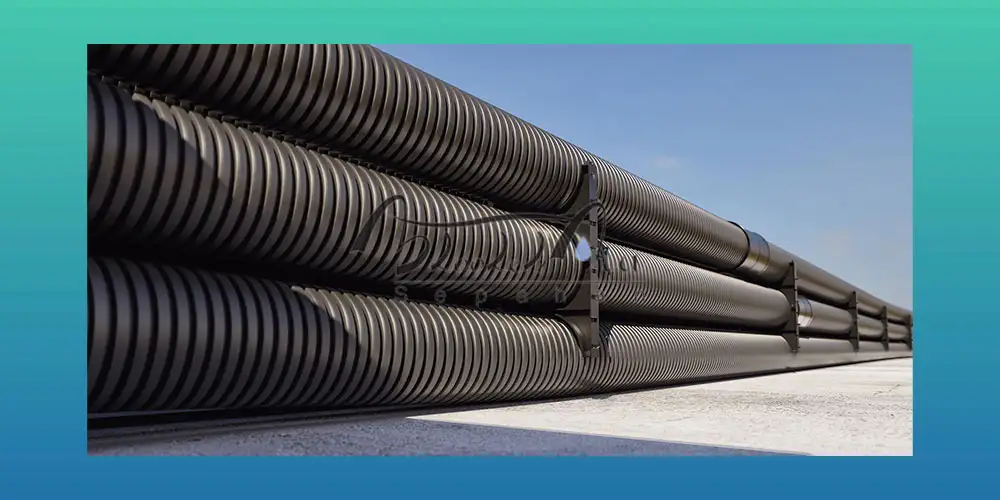
از تئوری تا اجرا – مهندسی خطوط لوله پلی اتیلن نفت و گاز
در این بخش، پایه های اساسی برای ساخت یک خط لوله پلیاتیلن سنگین (HDPE) موفق را بررسی میکنیم؛ از استانداردهای جهانی گرفته تا هنر اجرای آن در میدان عمل.
پایبندی به استانداردهای جهانی لوله فشار قوی
عملکرد مطمئن این لوله ها در گروی پیروی از استانداردهای شناخته شده جهانی است:
- استاندارد API 15LE: این یک استاندارد تخصصی از سوی انجمن نفت آمریکا (API) است که مشخصاً برای کاربرد لوله های پلیاتیلن در سرویس نفت و گاز تدوین شده.
- استانداردهای ASTM F714 و D3350: این استاندارد ها که توسط انجمن مواد و آزمون آمریکا (ASTM) ارائه شده، ویژگی های ابعادی و مشخصات فنی مواد اولیه را با دقت تعیین میکنند.
- استانداردهای ISO 4427 / 4437: اینها استانداردهای سازمان بینالمللی استانداردسازی (ISO) برای کاربردهای آبرسانی و گازرسانی هستند. نکته بسیار مهم: لازم به ذکر است که هرچند اصول کلی در طراحی لوله آبرسانی پلی اتیلن و لولههای نفت و گاز مشابه است، اما الزامات مربوط به مواد، آزمونها و ضرایب ایمنی برای کاربردهای هیدروکربنی به مراتب سختگیرانهتر است.
نقشه راه مهندسی: اصول کلیدی در طراحی
- انتخاب نسبت ابعاد استاندارد (SDR): این پارامتر که از تقسیم قطر خارجی بر ضخامت دیواره به دست میآید، تعیین کننده اصلی فشار قابل تحمل لوله است. مقدار پایینتر SDR به معنای دیواره ضخیم تر و در نتیجه، فشار کاری بالاتر میباشد.
- در نظر گرفتن ضریب کاهش دما: استحکام پلی اتیلن با افزایش دمای سیال کاری کاهش مییابد. به همین دلیل، برای دماهای بالاتر از ۲۰ درجه سانتیگراد، فشار قابل تحمل اسمی لوله باید در ضریب کاهش متناسب با آن دما ضرب شود تا ایمنی سیستم تضمین گردد.
- ملاحظات مربوط به دفن: طراحی عمق دفن، انتخاب نوع خاکریز و میزان تراکم آن، برای محافظت از لوله در برابر بارهای خارجی و فشارهای ترافیکی، اهمیت حیاتی دارد.
تکنیک های نوین نصب لوله های فشار قوی نفت
علاوه بر نصب سنتی در کانال باز (Open-Trench)، انعطافپذیری ذاتی پلیاتیلن سنگین، امکان بهرهگیری از روشهای مدرن بدون حفاری (Trenchless) را فراهم میآورد:
- حفاری جهتدار افقی (HDD): برای عبور دادن خط لوله از زیر موانعی چون رودخانه ها و جاده ها بدون نیاز به شکافتن سطح زمین.
- لغزشدهی (Slip-lining): راهکاری برای بازسازی خطوط لوله قدیمی که طی آن، یک لوله پلیاتیلن جدید به درون لوله قدیمی کشیده میشود.
- شکستن لوله (Pipe Bursting): روشی برای جایگزینی خطوط لوله قدیمی که در آن، لوله قدیمی همزمان با کشیده شدن لوله جدید پلیاتیلن، شکسته و از مسیر خارج میشود.
بازرسی و کنترل کیفیت (تایید نهایی)
فرآیند کنترل کیفیت شامل بازرسی مواد اولیه، کنترل دقیق پارامترهای تولید، بازرسی چشمی لوله ها، ثبت و کنترل داده های دستگاه های جوش فیوژن و در نهایت، اجرای آزمون فشار هیدرواستاتیک پس از نصب است تا از یکپارچگی و عملکرد بینقص کل سیستم اطمینان حاصل شود.
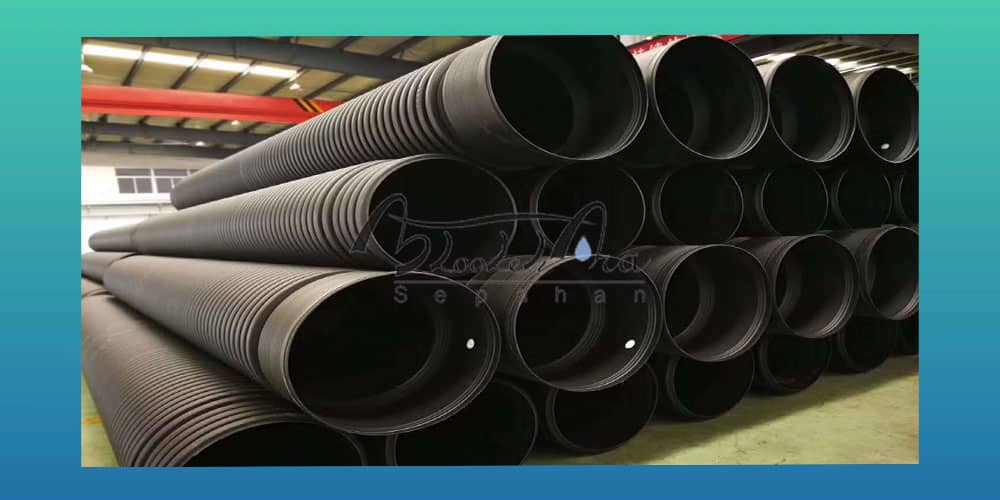
کاربرد های تخصصی لوله پلی اتیلن نفت و گاز
- خطوط جمعآوری (Gathering Lines): جهت جمعآوری نفت خام، گاز طبیعی و آب از سر چاهها و انتقال آنها به واحدهای فرآوری اولیه.
- سیستمهای توزیع گاز: به علت ایمنی بالا و مقاومت عالی در برابر خوردگی، به شکل گسترده در شبکههای توزیع گاز شهری استفاده میشوند.
- خطوط تزریق و دفع آب: برای تزریق آب یا دیاکسید کربن در پروژههای ازدیاد برداشت (EOR) و همچنین برای دفع آب تولیدی شور و خورنده (SWD).
- کاربردهای فراساحلی: به دلیل مقاومت ممتاز در برابر آب دریا، برای انتقال سیالات بین سکوها، خطوط آبگیر و خطوط دفع پساب گزینهای ایدهآل هستند.
- بازسازی خطوط لوله: به عنوان یک راهکار اقتصادی، سریع و مطمئن برای نوسازی و احیای زیرساختهای فرسوده و قدیمی.
استانداردها، طراحی و ملاحظات اجرایی
۴.۱. استانداردهای بینالمللی کلیدی
تولید و استفاده از لوله های HDPE باید مطابق با استاندارد های معتبر انجام شود:
- API 15LE: استاندارد تخصصی انجمن نفت آمریکا برای لوله های پلی اتیلن در سرویس نفت و گاز.
- ASTM F714, D3350: استانداردهای انجمن مواد و آزمون آمریکا برای مشخصات ابعادی و مواد اولیه.
- ISO 4427 / 4437: استانداردهای سازمان بینالمللی استاندارد سازی برای کاربرد های آبرسانی و گازرسانی. لازم به ذکر است که هرچند اصول کلی در طراحی لوله گازرسانی و لولههای نفت و گاز مشابه است، اما الزامات مواد، تست ها و ضرایب ایمنی برای کاربرد های هیدروکربنی به مراتب سخت گیرانه تر است.
۴.۲. اصول طراحی خط لوله HDPE
- انتخاب SDR: نسبت ابعاد استاندارد (SDR) که از تقسیم قطر خارجی بر ضخامت دیواره به دست میآید، تعیینکننده فشار قابل تحمل لوله است. SDR پایین تر به معنای دیواره ضخیم تر و فشار کاری بالاتر است.
- ضریب کاهش دما (Derating Factor):
با افزایش دمای کاری سیال، استحکام پلی اتیلن کاهش مییابد. برای دماهای بالاتر از ۲۰ درجه سانتیگراد، فشار قابل تحمل اسمی لوله باید در ضریب کاهش متناسب با آن دما ضرب شود. - ملاحظات دفن:
طراحی عمق دفن، نوع خاکریز و تراکم آن برای محافظت از لوله در برابر بارهای خارجی و ترافیکی حیاتی است.
۴.۳. تکنیک های نصب علاوه بر نصب سنتی در کانال باز (Open-Trench)، انعطاف پذیری HDPE امکان استفاده از روش های مدرن بدون حفاری (Trenchless) را فراهم میکند:
- حفاری جهت دار افقی (HDD):
برای عبور از موانعی مانند رودخانه ها و جاده ها . - لغزش دهی (Slip-lining): برای بازسازی خطوط لوله قدیمی با کشیدن یک لوله جدید HDPE به داخل لوله قدیمی.
- Pipe Bursting:
برای جایگزینی خطوط لوله قدیمی با شکستن لوله قدیمی و کشیدن همزمان لوله جدید HDPE.
۴.۴. بازرسی و کنترل کیفیت (QC/QA) کنترل کیفیت شامل بازرسی مواد اولیه، کنترل پارامتر های تولید، بازرسی چشمی لوله ها، ثبت و کنترل داده های دستگاه های جوش فیوژن و انجام تست فشار هیدرواستاتیک پس از نصب برای اطمینان از یکپارچگی کامل سیستم است.
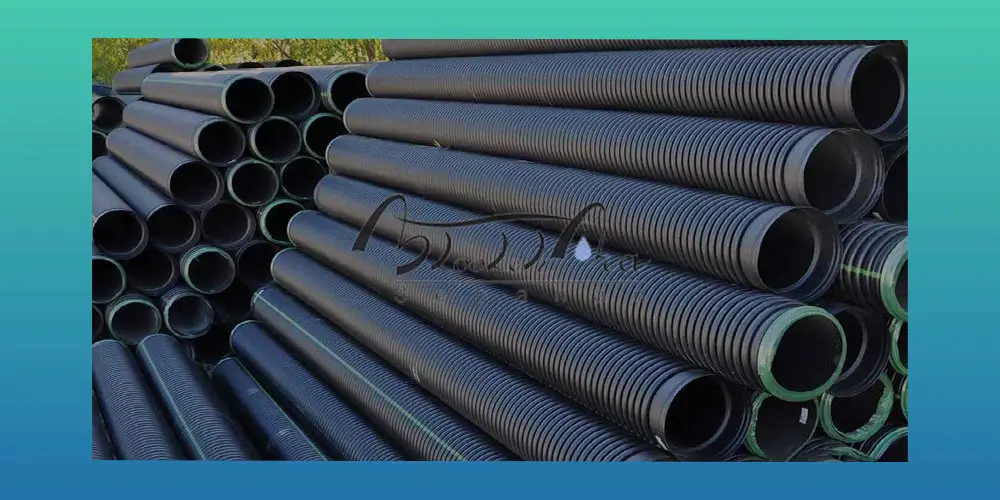
تحلیل تطبیقی برای کاربردهای نفت و گاز
در صنعت نفت و گاز، انتخاب بین لولههای HDPE و فولاد کربنی تنها یک گزینه تکنیکی نیست؛ این تصمیم معیارهایی از قبیل خوردگی در محیط سولفیدی، تناژ حمل و نقل ، فشار کاری بالا و هزینه های کل چرخه عمر را دربرمیگیرد. در این بخش، با نگاهی تخصصی به نیازهای پروژههای نفت و گاز، مسیر درست را نشان میدهیم.
۱. معیار های فنی ویژه نفت و گاز
مقاومت به خوردگی سولفیدی و CO₂: آیا لوله در مواجهه با H₂S و CO₂ خورندگی الکتروشیمیایی را تحمل میکند؟
ظرفیت فشار بالا: تا چه فشاری (مثلاً 16–20 بار یا بیشتر) میتوان روی لوله حساب کرد؟
کیفیت اتصالات در شرایط پرترافیک میدان: آیا اتصالات در دمای پایین یا شرایط حفاری فرکچر مستحکم باقی میمانند؟
سایش ناشی از ذرات حفاری: در سیالات دوغابی حاوی برادههای سنگ و ماسه، دوام چه گزینهای بیشتر است؟
ثبات هیدرولیکی تحت جریان متناوب چاه: افت فشار در پمپاژ مکرر و جریان پلکانی چگونه تغییر میکند؟
۲. مقایسه تکنیکال: لوله پلی اتیلن فشار قوی در برابر فولاد کربنی در نفت و گاز
معیار | لوله فشار قوی (نفت و گاز) | فولاد کربنی |
---|---|---|
خوردگی H₂S/CO₂ | بدون نیاز به حفاظت الکتروشیمیایی—کاملاً مقاوم | نیازمند پوشش های داخلی/حفاظت کاتدی مداوم |
فشار کاری | تا 16–20 بار استاندارد، با گرید PE100-RC | تا 50 بار بالقوه، ولی هزینه ساخت و نصب بالاست |
اتصالات در شرایط میدان | جوش بات / الکتروفیوژن،یکپارچگی پایدار زیر صفر°C | جوش سنتی و فلنج، احتمال نشتی در دماهای پایین |
سایش دوغاب حفاری | مقاومت بالا در برابر ذرات ساینده | کاهش ضخامت سریع تر و کارآمدی کمتر |
پایداری هیدرولیکی | ضریب Manning n≈0.009 ثابت در طول عمر | زبری افزایش پاینده با خوردگی و رسوب |
طول عمر مفید | بیش از ۵۰ سال در شرایط عملیاتی | معمولاً ۲۵–۳۵ سال با تعمیرات مکرر |
۳. تحلیل اقتصادی با رویکرد TCO در نفت و گاز
CAPEX (سرمایه ای)
لوله های فشار قوی: هزینه متوسط مواد، حمل سبک تا میدان های دورافتاده، نصب سریع با حداقل تجهیزات حفاری
فولاد: قیمت بالا، انتقال پیچیده، نیاز به جرثقیل و نیروی متخصص
OPEX (عملیاتی)
HDPE: حذف هزینه های حفاظت خوردگی، کاهش مستمر هزینه انرژی پمپاژ در جریان های متناوب چاه
فولاد: نگهداری پوشش داخلی، تزریق مواد بازدارنده، بازررسی های دورهای پرهزینه
نتیجهگیری اقتصادی: در پروژههای نفت و گاز، HDPE میتواند تا ۳۰–۴۰٪ کاهش TCO نسبت به فولاد کربنی به همراه آورد، بهویژه در حوزههای offshore و میدان های دارای سیال خورنده.
۴. توصیه های کاربردی برای پروژه های نفت و گاز
میدانهای حاوی H₂S/CO₂: استفاده از لولههای PE100-RC با پوشش کربنبلک برای بیشترین پایداری.
فشار بسیار بالا (بالای 20 بار):
ترکیب لوله HDPE در خطوط فرعی و فولاد کربنی در حلقه های اصلی برای بهینه سازی هزینه.چالشهای لجستیکی در offshore:
بهدلیل وزن سبک و انعطافپذیری HDPE، جابهجایی و نصب لوله ها سریع تر و اقتصادی تر صورت میگیرد.گام بعدی: انجام شبیه سازی TCO بر اساس عمق چاه، دما، فشار و ترکیبات شیمیایی میدان.
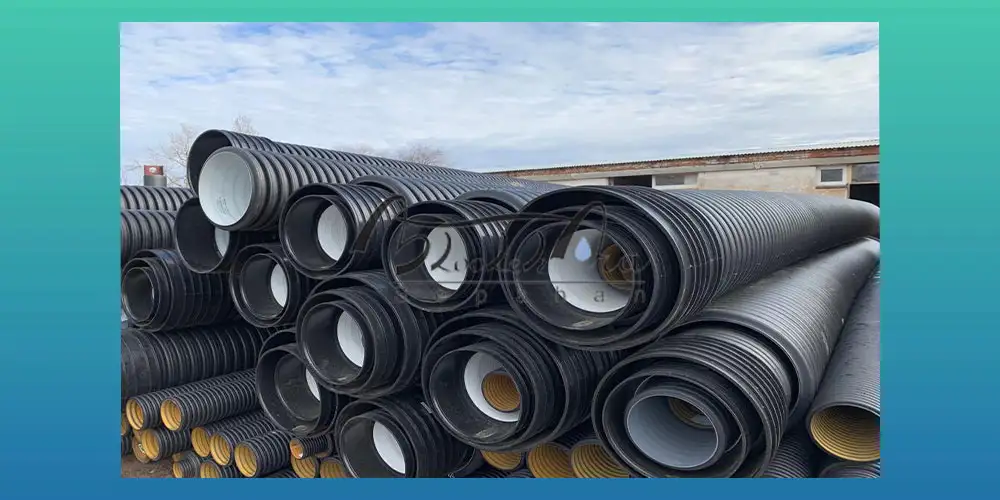
نتیجهگیری نهایی برای زیر ساخت های نفت و گاز
برتری فنی در محیطهای خورنده: لوله فشار قوی پلی اتیلن نفت با مقاومت ذاتی در برابر H₂S، CO₂ و آب شور، محافظ قابل اعتمادی است که نیاز به پوشش های پیچیده و حفاظت کاتدی را بهکلی حذف میکند.
عملکرد بلندمدت و یکپارچگی: عمر مفید بیش از ۵۰ سال، اتصالات مونولیتیک بدون نشتی و انعطاف پذیری بالا، تضمین میکند سیستمهای پالایشگاهی، خطوط فرعی و انتقال نفت خام در میدانهای onshore و offshore بهطور پیوسته و ایمن کار کنند.
صرفهجویی اقتصادی عمیق: کاهش ۳۰–۴۰٪ در کل هزینه مالکیت (TCO) از طریق پایین آوردن CAPEX (حمل و نصب سبک، تجهیزات کمتر) و OPEX (حذف هزینه های خوردگی و کاهش مصرف انرژی پمپاژ) بهویژه در پروژه های بزرگ نفت و گاز.
انتخاب استراتژیک آینده نگر : با تمرکز صنعت نفت و گاز بر ایمنی، پایداری محیط زیست و بهره وری اقتصادی،لوله پلی اتیلن فشار قوی نفت و گاز نه یک جایگزین بلکه یک استاندارد جدید برای زیر ساخت های انتقال و توزیع هیدروکربن ها خواهد بود.